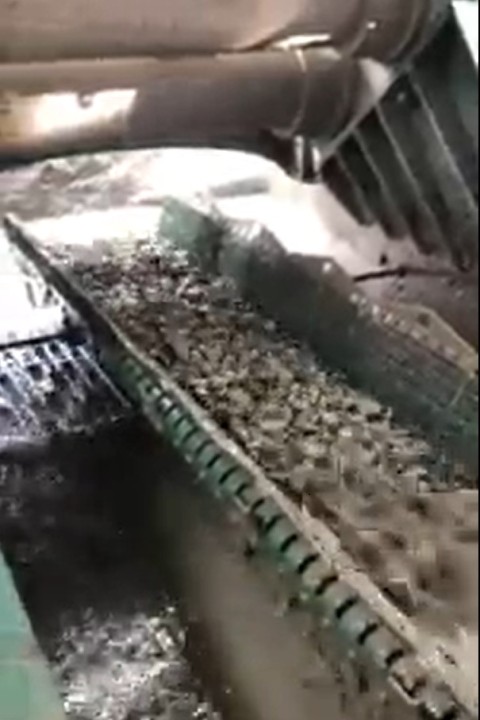
The process of horizontal directional drilling (HDD) inevitably produces a large amount of liquid waste. Drilling fluid returns from the drill head assembly a mixed slurry of water, chemical additives, and entrained spoils generated from within the borehole. This difficult waste challenge is best tackled by implementing an optimized mud recycling / solids control system on site.
As the HDD industry has grown and the engineering behind drilling fluid design has improved, the need for proper drilling fluid management has come to the forefront. It has become obvious that the economics behind drilling fluid maintenance and disposal are such that the ability to recover and recycle is mission critical. The primary driving factors behind the rise of mud recycling / solids control include:
- Reduced Waste Disposal Costs
- Reduced Green House Gas Emissions
- Reduced make-up water
- Reduced fluid additive costs
- Improved drilling fluid rheology
- Reduced equipment maintenance costs
Reducing Waste Disposal Costs
Discarding used drilling fluid without an optimized mud recycling / solids control program is an outdated and cost prohibitive business model. It is also clear that industry standards and expectations are changing such that transporting loads of wet drilling waste in vacuum trucks to Class II waste disposal facilities does not have good optics. A well-executed drilling fluid recovery program results in a drastic reduction in waste volume by dewatering the cuttings. In fact, solids control equipment can eliminate cuttings waste by reclassifying it as a dry product for reuse on site as spreadable soil.
Reducing Green House Gas Emissions
The larger the HDD drill, the more volume of waste created. Depending on the size of the project, mud volumes can range from 1,000 m3 to 5,000 m3 depending on the scope of the project. Hauling large volumes of fluid in vacuum trucks to be disposed of at a wet waste disposal facility results in large amount of unnecessary GHG emissions. Equally concerning are the loads of make-up water required to continually replenish the drilling fluid volume hauled away. Eliminating semi-truck loads of water and fluid is a massive win economically and environmentally for all parties involved.
Example:
In a recent HDD Direct Pipe installation in B.C, a contractor chose an optimized mud recycling system which removed 1,018 m3 of dry cuttings from the drilling fluid over the span of 8 days. These dry cuttings were then spread onsite. A rough calculation can be done to estimate the reduction of produced C02 by processing the drilling fluid on site rather than hauling it for disposal at a Class II disposal facility.
Note: Reduction of fluid retention on cuttings was >90% after passing through the mud recycling system.
Total Volume of wet cuttings = (Dry Cuttings) x (Fluid Retention on Cuttings w/o mud system)
Total Volume of wet cuttings = 1,018 m3 x 1.90 = 1,934 m3
Total Semi-vac Loads = 1,934 m3 / 23 m3 = 84 loads
Volume of Diesel fuel burned = 84 loads x 400 km round trip x 39.5 liters/100 km
Volume of Diesel fuel burned = 13,272 Liters
Volume of C02 produced = 2.7 kg C02 / liter x 13,272 liters = 35,834 kg of C02
By utilizing this solids control system, the contractor reduced the carbon footprint of this project by at least 35,834 kg of CO2 (excluding idling onsite while loading, hauling of make-up water etc.).
To offer some perspective, the average Canadian vehicle produces 4,600 kg of C02 per year. In this specific example, the contractor’s decision to choose an optimized mud recycling solution was the equivalent of removing 8 Canadian cars off the road in 2022 over the span of an 8-day project!
Reducing Fluid Additive Costs
Drilling fluid is the lifeblood of an HDD drilling operation, and many companies now employ Mud Testers to actively sample mud onsite while drilling. Drilling fluid is specified according to the ground conditions and types of soils present throughout the length of the drill. Depending on the desired mud weight, viscosity, and gel strength many different chemical additives must be added including clay minerals (bentonite), polymers (PAC), surfactants and Soda Ash to maintain optimal drilling conditions. The ratio of fluid loss on cuttings is directly correlated to the volume of additives required to maintain the desired drilling fluid properties. An optimized mud recycling system drastically reduces fluid on cuttings which in turn reduces raw materials required on site.
Improved Drilling Fluid Rheology
One of the most important objectives of a mud recycling system / solids control equipment is to remove as much drilled solids as possible on the first pass through the system. Solids that are not removed during this initial pass are broken down into finer particles by the drill bit, reamers, and mud pumps. An accumulation of fines in the system inevitably leads to the degradation of the mud rheology as mud weight increases and becomes increasingly difficult to manage. Fortunately, with an understanding of particle size distribution within a mud slurry, mechanical separation equipment can be optimized to selectively reject undesirable formation solids and retain the specified drilling fluid properties.
Reducing Equipment Maintenance Costs
When it comes to mud pumps, drill bits and other fluid transport equipment, abrasion is the enemy. Suspended soil and rock particles in the drilling fluid can have a massive impact on the degradation of impeller blades, mud motor components and jet assemblies. Additional tool wear can be avoided with a properly designed and optimized reclaimer equipment which removes all unwanted fines from the drilling fluid slurry.