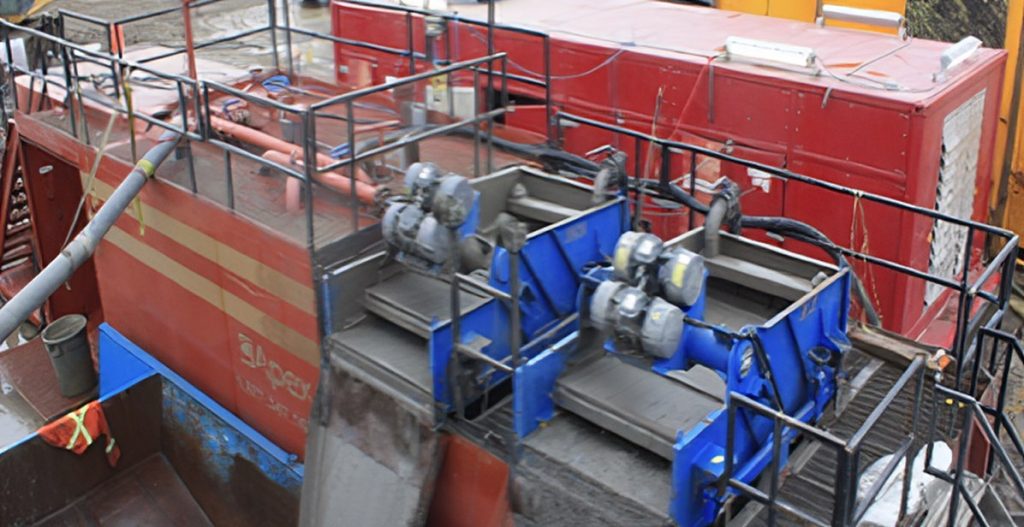
Fresh water usage, trucking costs, GHG emissions, legacy costs; these are all buzzwords that businesses across all industries are aiming to eliminate from their operations. When it comes to the drilling industry in particular, water re-use and recycling are increasingly vital to operators. Whenever a process produces large volumes of liquid waste, the ability to recover and recycle as much fluid from that waste stream as possible becomes mission critical. This is where a fully optimized “closed-loop” fluid recycling /solids control system comes in to play.
Closed Loop System in Oil and Gas
In Canada, the oil and gas industry has already been using closed-loop systems for recycling their drilling fluids for decades. This trend has eliminated the use of sumps and allowed for reuse of drilling fluids over multiple wells. The closed-loop design ensures the drilling fluid never touches the ground, which is truly a massive reduction in environmental disturbance.
A Typical Closed Loop System
The typical closed-loop system on a drilling rig consists of a multi-stage process where flow from the bore is first split across multiple shakers. The shakers are the first line of defense within the solids-control system and are used to effectively separate the free fluid from the larger cuttings. The basic shaker design consists of large, flat sheets of wire mesh vibrating screens. Depending on the application, either linear or tuned elliptical vibrating motion is used to move the cuttings across the screen while allowing the drilling fluid to pass through them. Dried cuttings are discharged at the end of the shaker where they slide down to a containment bin below.
The second phase of a closed-loop solids control system consists of removing low gravity solids from the drilling fluid using centrifuges. Centrifuges use forces of 300 to 3,500 G to remove fine particles, down to a size of 5 microns. Through proper optimization of the centrifuges, the integrity of the drilling fluid is maintained and circulated back to the drilling rig for re-use.
As drilling rates become faster and more finely engineered drilling fluid become commonplace, the importance of higher-capacity shakers, bigger centrifuges and an optimized solids control system has come to the forefront. High volume “big bowl” centrifuges now dominate the solids control market. These centrifuges can remove 2-8 tons of solids per hour and can reduce low gravity solids in the drilling fluid to below 5% with chemical assistance.
Advantages of a Closed-Loop System:
- Well Construction Costs: Using a Closed-Loop system prevents the construction cost of building a lined pit.
- Footprint: A traditional pit system requires a much larger footprint. Using a Closed-Loop system allows the rig to maintain a smaller Environmental footprint.
- Water Savings Costs: Water must be transported to the rig which is not usually closely situated to drilling location. A Closed-Loop system can reduce water consumption by the reuse of treated water on site, which in turn reduces transportation costs.
- Drilling Fluid Costs: The costs of drilling fluids can very based upon the chemical properties needed for each well. Use of a Closed-Loop system allows for reuse of drilling fluids which in turn decreases the amount of drilling fluid additives required to maintain fluid properties.
- Environmental Impact: Use of a Closed-Loop system reduces the Environmental Hazard Potential of traditional pit. Traditional pit liners may leak, heavy rains can cause an overflow from a traditional pit, which in turn can be an Environmental Hazard to the soils and water table.
- No Legacy Costs: The alternative to a closed-loop system is a digging and lining a sump for fluid containment. Legacy costs of a sump can include continued monitoring and site testing to ensure proper containment.