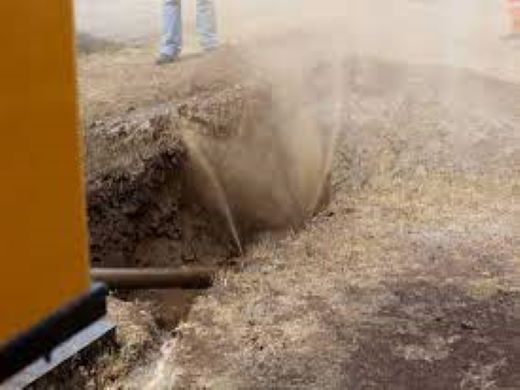
The evolution horizontal directional drilling (“HDD”) can be traced back into the early 1900’s. In those days it became known within the oil industry that small deviations in vertical wellbores were happening due to dips and faults in the rock strata, increased weight on bit and the drill strings’ ability to bend. With the development of magnetic survey equipment, controlled directional drilling became a reality which in turn spawned the era of HDD drilling. Over the past three decades HDD drillers have continued to adopt best practices from the oil and gas industry to increase efficiency by any means possible. The competitive nature of the industry eventually led to the spotlight landing on the lifeblood of all HDD operations, the drilling fluid (aka drilling mud).
Originally HDD drillers used strictly water as their drilling fluid. At the time, existing engineered drilling mud had only been designed and marketed to conventional vertical drilling. As a result, HDD drillers experienced many avoidable issues such as stuck pipe, high wear and frequent downtime that plagued operations. However, this has begun to change with the recognition that the right drilling fluid can have a massive impact on the success of an HDD project. A properly designed drilling fluid is one that performs many functions including:
- Cuttings Removal
- Borehole Stability
- Lubricating and Cooling the Drill Bit
Cuttings Removal
During the HDD drilling process cuttings are generated and must be removed from the hole. To remove cuttings, drilling mud is circulated through the drill string and bit after which it carries the produced cuttings to surface through the annulus of the bore hole. The effectiveness of the cutting’s removal is in part correlated to the drilling fluids viscosity. Viscosity can be described as a fluid’s “thickness” or resistance to flow. In general, the higher the viscosity, the better it will suspend cuttings during transport. This is especially important for HDD drilling as a low viscosity mud will result in cuttings settling out and accumulating on the low side of the bore hole. This accumulation of cuttings restricts flow and increases the torque required during drilling. Speaking of increased torque, it is important to note that an excessively high viscosity is equally detrimental to drilling. Since a highly viscous fluid will be more resistant to flow, a higher pumping pressure is required to maintain circulation.
Cutting’s removal in HDD drilling is also highly dependent on gel strength. HDD drilling fluids are designed to be shear-thinning and thixotropic, which means they become less viscous under shear pressure but will gel under static conditions. As the bit or reamer cuts the bore path it also mixes the soil into a slurry with the fluid. The gel strength of the fluid is responsible for keeping the cuttings in suspension at reduced velocities or in the event circulation stops.
Borehole Stability
One of the functions of a drilling fluid is to coat the walls of the borehole with a layer known as the filter cake. The filter cake acts as a sealant to stabilize the bore hole and reduce the amount of water loss into the formation. Drilling fluid properties are specifically designed for the geology of the soil/formation being drilled. For example, in a highly porous and permeable sand formation the filter cake is extremely important to keep the bore hole stable. Without the filter cake barrier water flows directly into the formation resulting in the collapse of the bore hole behind the tooling. The rheology of highly reactive clays that swell when in contact with water pose a whole myriad of challenges as well. Once again drilling fluid properties must be adjusted with the addition of synthetic polymers to prevent the clays from soaking up water. Ideally a good HDD drilling fluid should be matched with the soil conditions to form a thin impermeable filter cake to maintain borehole stability.
Lubricating and Cooling the Drill Bit
Frictional heat is generated at the drill bit face and must be dissipated by the constant circulation of drilling fluid. In addition to cooling, the drilling fluid acts as a lubricant to reduce frictional force. Poor lubrication results in high torque, drag and abnormal wear on the drilling head and drill pipe.
Maintaining Drilling Fluid Properties
Without question, drilling fluid is extremely important to the success of all HDD drilling operations. An essential part of maintaining the desired drilling fluid properties is a quality mud recycling / solids control system. Spoils from the drilling head become suspended, by design, in the drilling mud slurry and must be removed. Optimization of a mud recycling system is done by engaging with a drilling fluid expert that will determine the required equipment, tankage, pumps, and operating parameters to maximize solids removal and maintain drilling fluid integrity. Many variables must be considered including anticipated geology, mud weights, viscosity, drilling rates and fluid volumes to determine the processes and equipment required. In short, there is no question that maintaining drilling fluid properties is essential in HDD drilling and the best way to achieve this is through an expertly designed and operated mud recycling / solids control system. A properly designed mud recycling system can save an HDD contractor money by reducing the cost of drilling fluid chemicals, make-up water and cuttings disposal. Consult with one of our drilling fluid experts today.